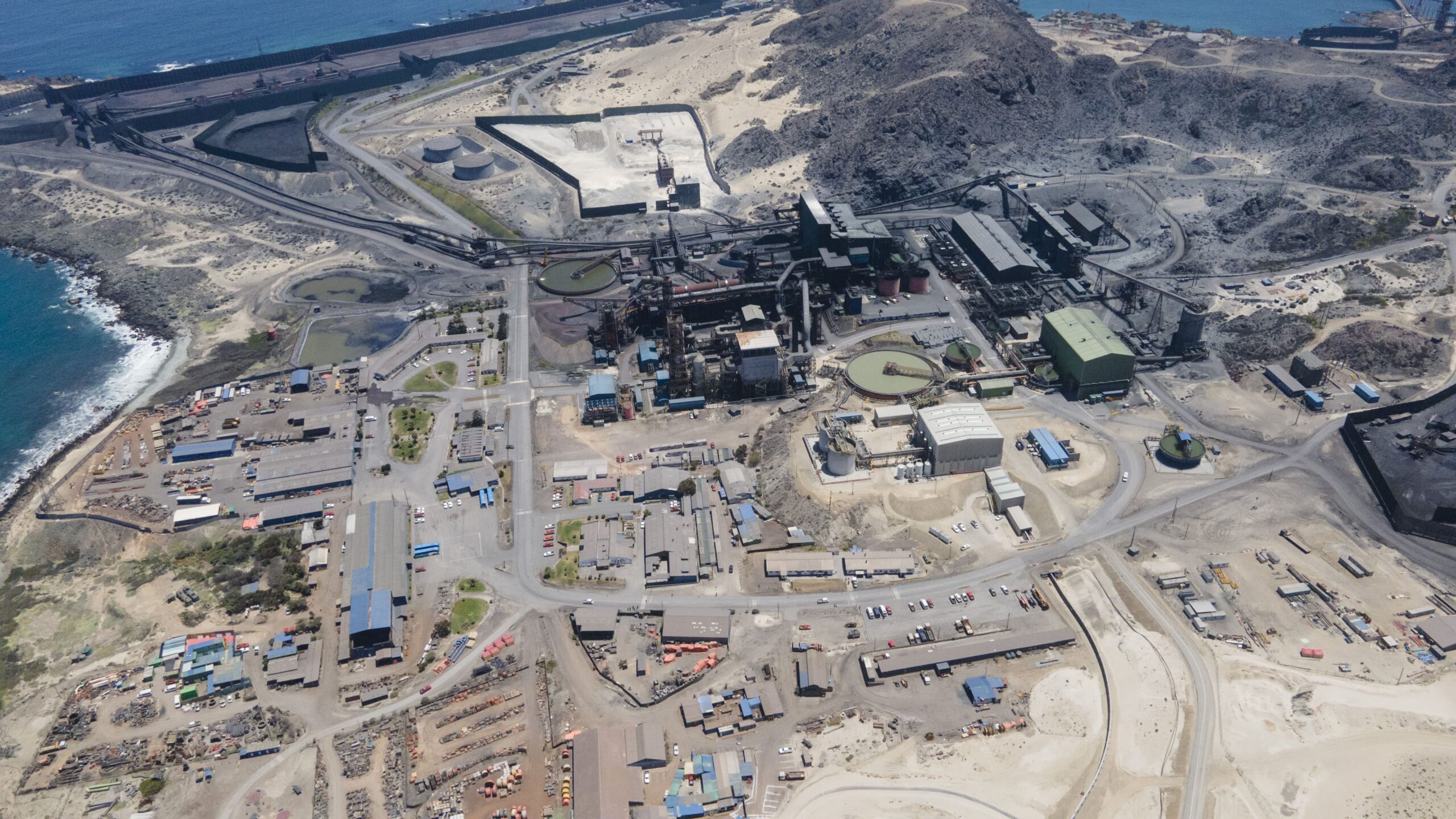
LOCATION
The Pellet Plant is located 5 kilometers from the port of Huasco. It was commissioned at the end of 1978, with a nominal capacity of 3.5 million tons of pellets per year. The ore fed to the process comes from Minas Los Colorados, where it is subjected to various stages of crushing and dry magnetic concentration, obtaining the product called preconcentrate. At the Pellet Plant, it is stored and homogenized in the reception courts. From there, it is sent selectively to the wet milling and magnetic concentration processes, with the purpose of reducing the particles to a particle size suitable for eliminating impurities and obtaining a specific surface suitable for pelletizing.
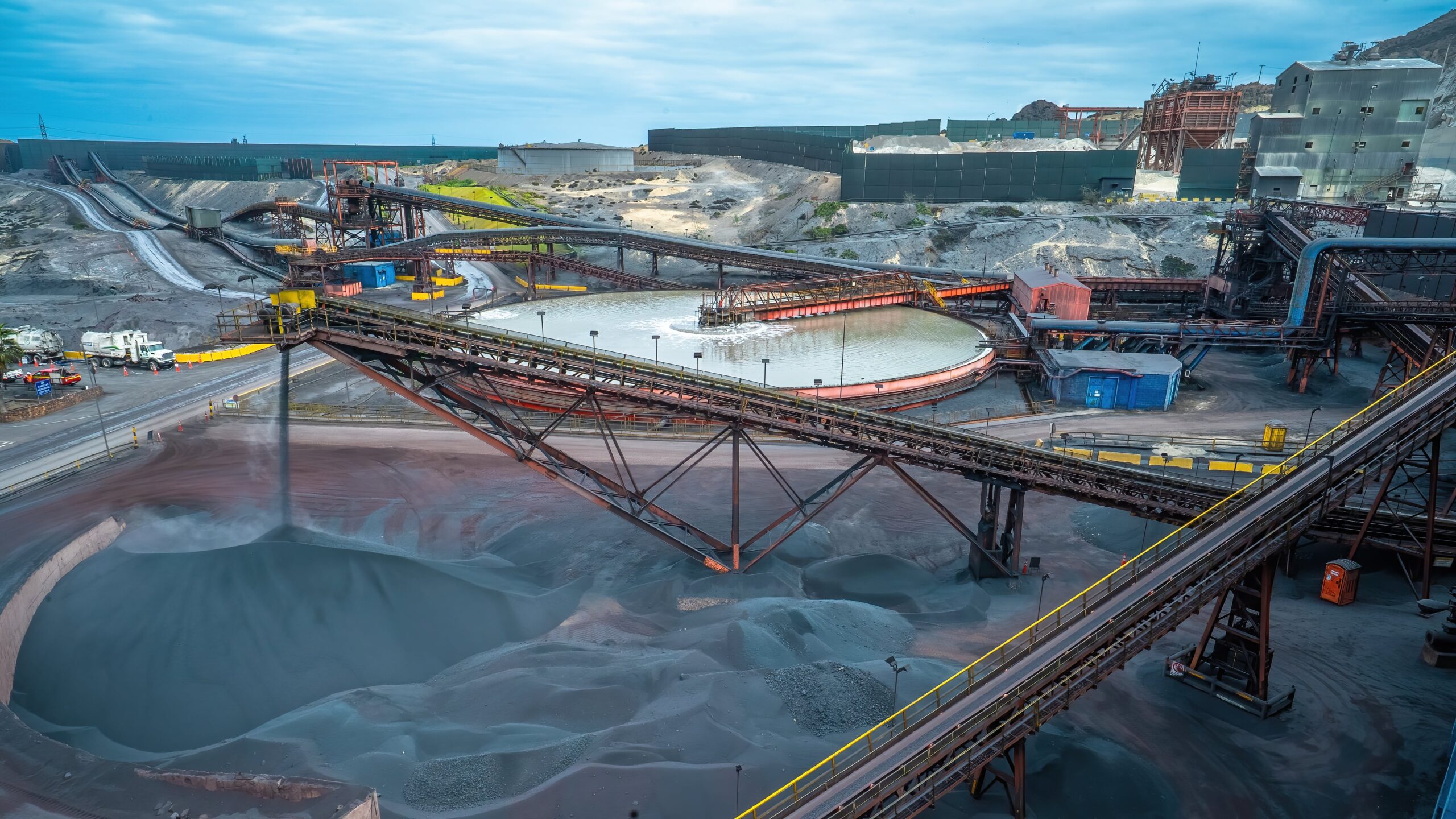
DIMENSIONS
The magnetic concentrate is filtered and then mixed with additives that act as binders in the pelletizing process and slag in the subsequent thermal hardening stage, to be finally pelletized into discs.
Since the start-up of the plant, continuous improvements have been made to the entire process, which have increased production, reduced specific consumption and diversified the products, reaching an annual production of 4 million tons of pellets for blast furnaces and direct reduction, and more than one million tons of pellet feed.
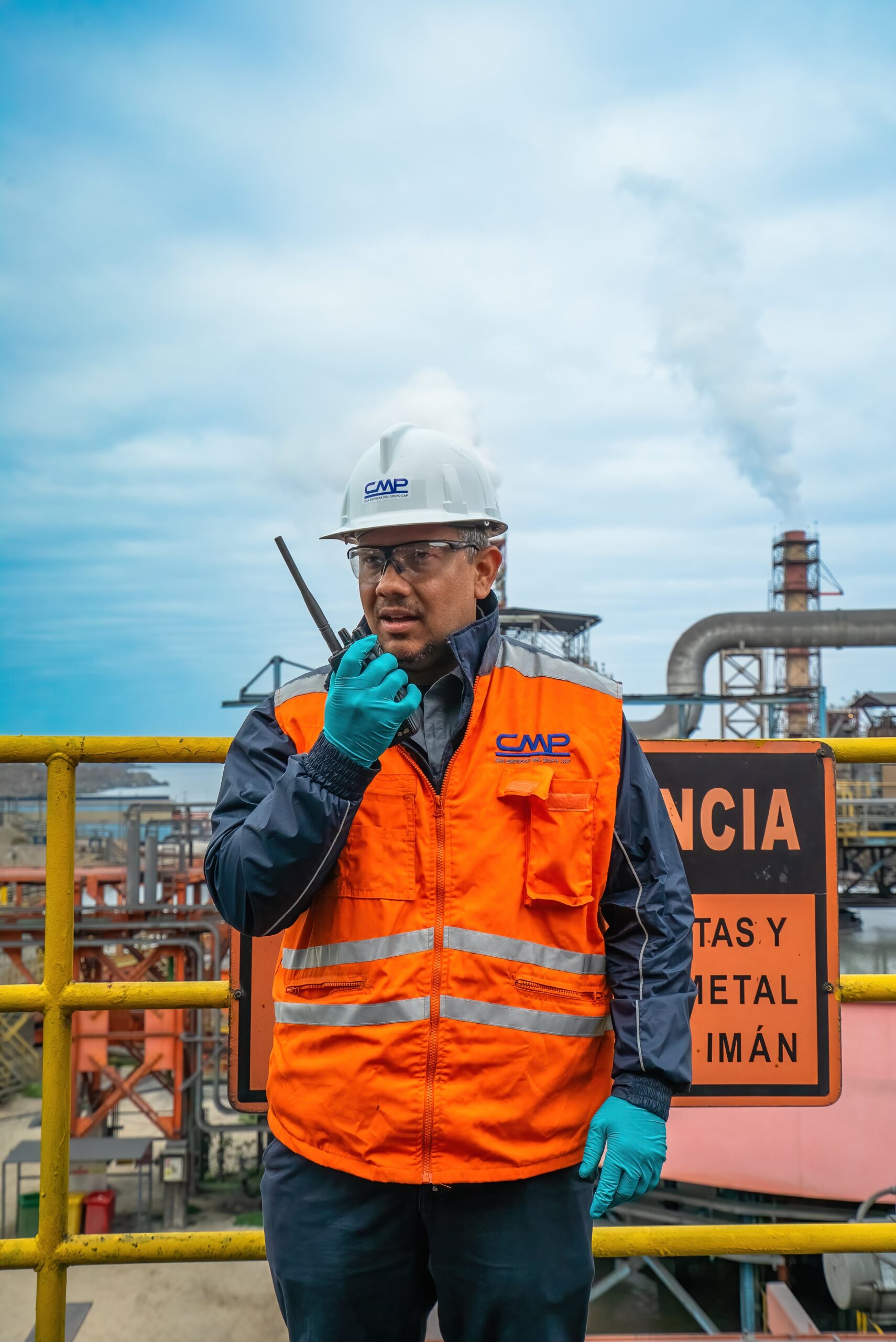
CERTIFICATION
The Pellets Plant is certified according to international standards ISO 9.001, ISO 14.001, OHSAS 18.001 and ISO 50.001, which leads the company to comply with world-class standards; that is why continuous improvement in quality, environmental and safety matters is essential in each of the plant’s processes.
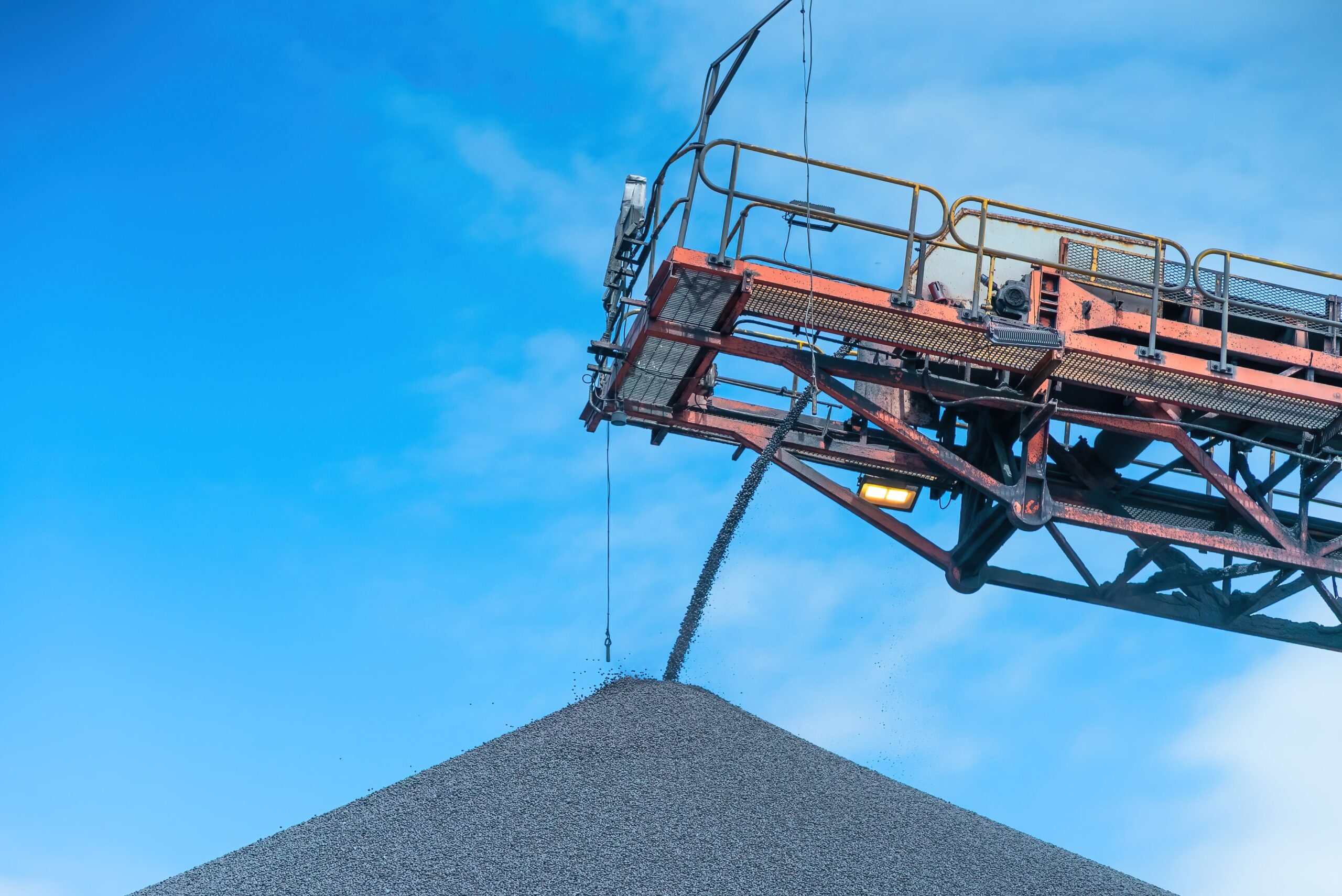
PRECONCENTRATE STORAGE
The pre-concentrate coming from the mine is stored and homogenized in a 500 thousand tons total capacity tank, according to its quality and destination. It is stockpiled in different piles of defined qualities for further processing.
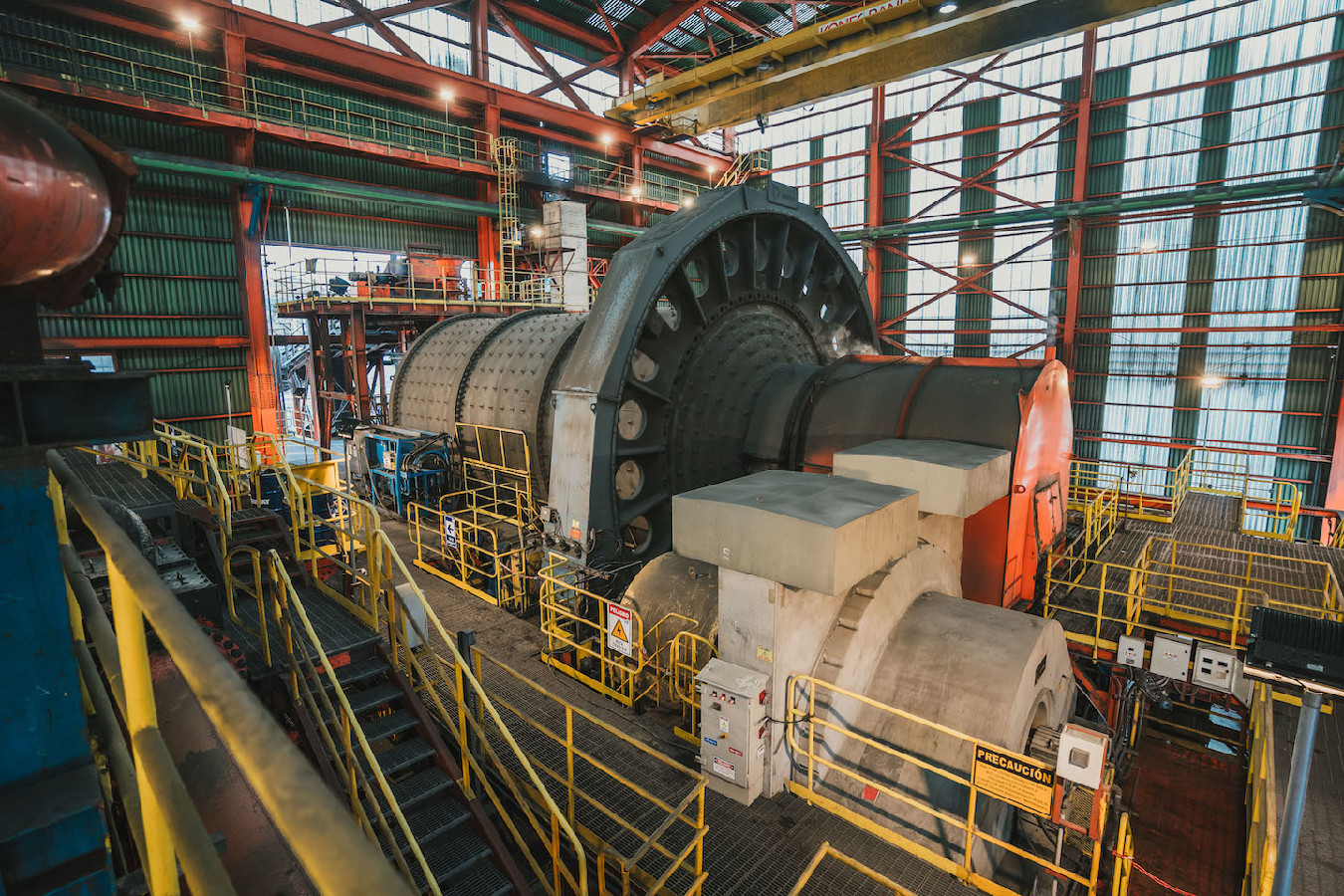
WET GRINDING AND CLASSIFICATION
The preconcentrate is transported from the stockpiles to the milling stage, which is currently composed of three lines, each with a 16.5 37.5 foot ball mill, with a 6,000 HP motor, in closed circuit with a battery of 6 hydrocyclones. The iron ore is reduced in size and classified to 80% below 44 microns.
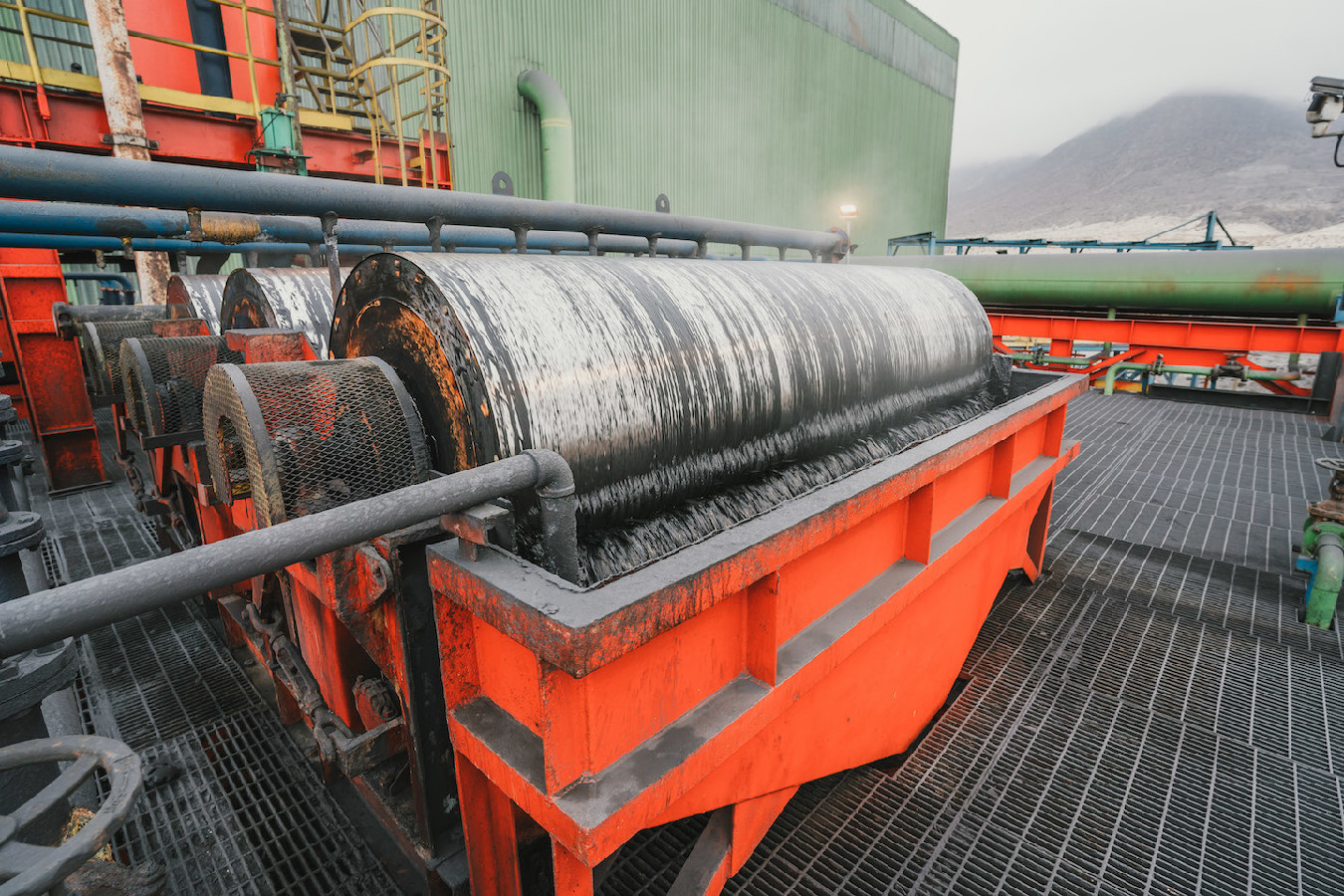
MAGNETIC CONCENTRATION
The concentrator has a set of batteries of 36″ diameter and 750 Gauss, and others of 48″ diameter and 1,000 Gauss, forming the primary concentration and reworking stages, generating a magnetic concentrate that is transferred to the next stage of filtration, and the tails are sent to a thickener where the water is recovered and the low flow is finally disposed of in a submarine outfall.
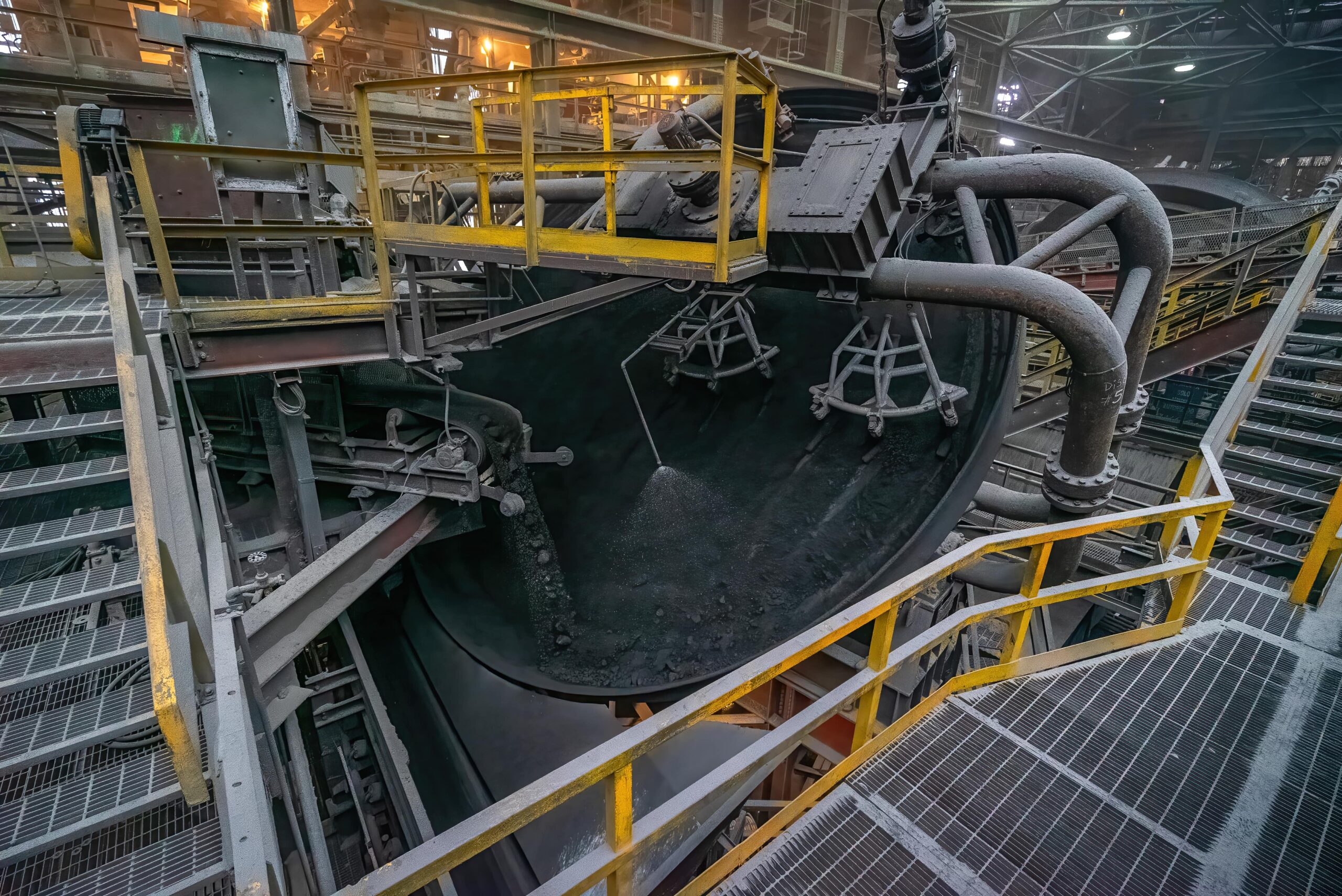
FILTERING AND BALLING
The concentrate is thickened; then it is transferred to the agitator tanks to be homogenized and later sent to the disc filtrate, where the product called Pellet Feed is obtained, which feeds the Balling process to produce the Pellets.
The filtered “cake” is mixed with an additive in an amount according to the type of pellets to be produced and the mixture is fed and transformed into green pellets in the pelletizing discs, passing later to the roller screeners, where they are selected according to their size.
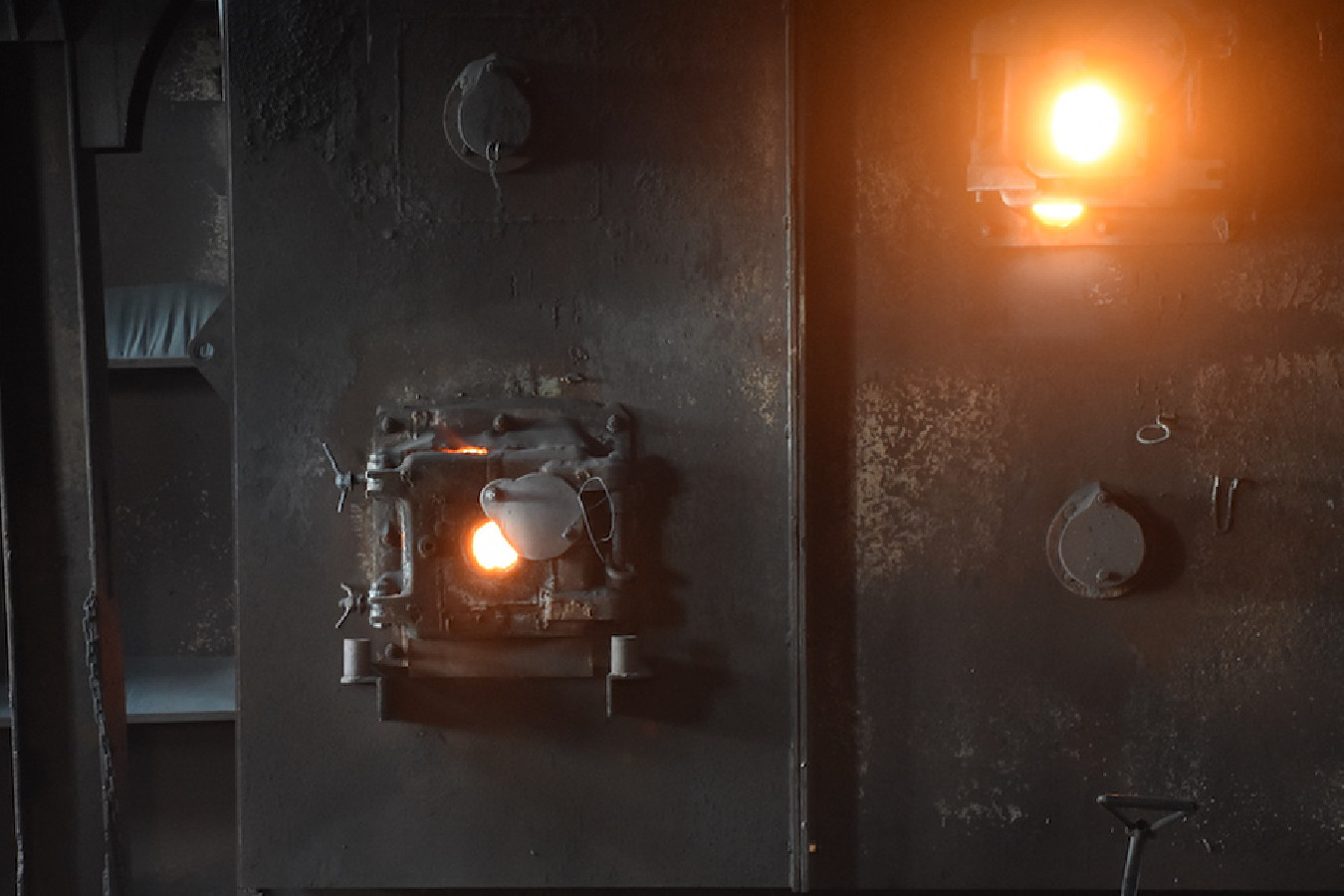
THERMAL HARDENING
The previously selected green pellets are dried and heated in the grate furnace to a temperature of 1,100 °C. They are then taken to the rotary kiln, where they are finally hardened at temperatures of approximately 1,300°C.
The glowing pellets are cooled a flow of air at ambient temperature in the annular cooler. The hot air obtained from the heat transfer is recovered to the rotary kiln and the grate kiln.
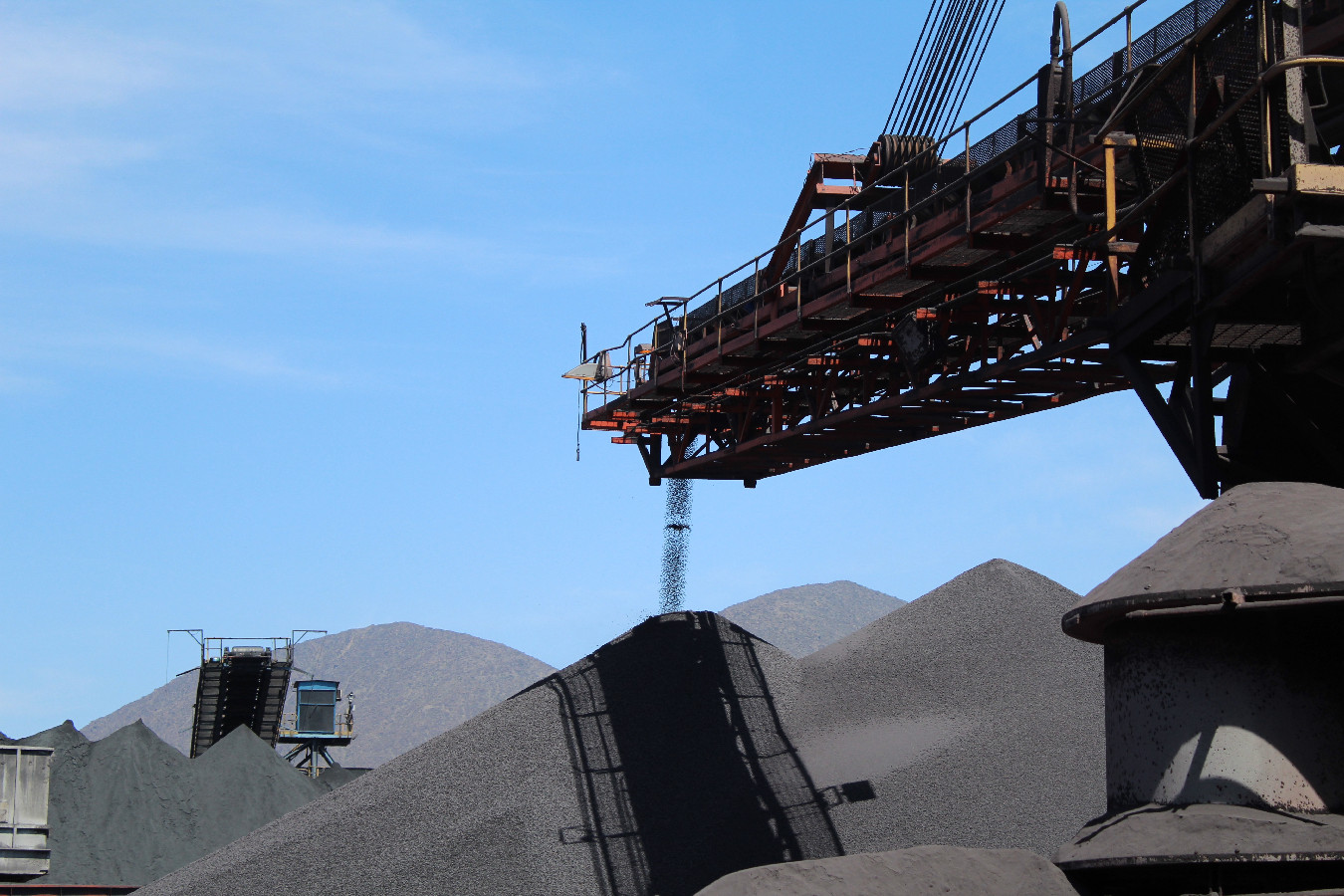
PELLET STORAGE
Pellets that have been cooled and sorted according to size are sent for storage to the product storage bins, where they are stacked a stacker according to quality.